통합공사로 조립 3라인 혼류 생산 전환
공장 효율성 높아져 시간 당 8대 더 생산 가능해져
KG 모빌리티가 지난 23일 경기도에 위치한 평택 공장에서 미디어 대상 초청 행사를 진행했다.
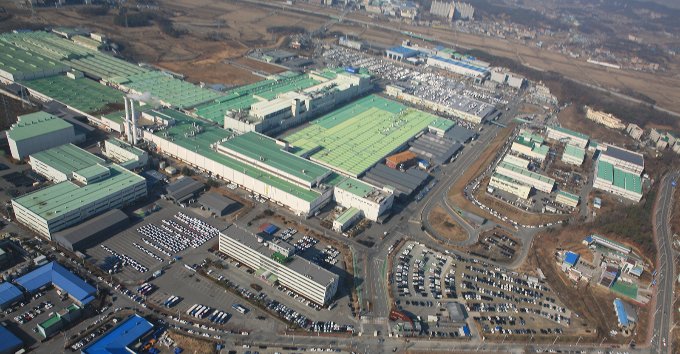
평택 공장은 86만m²(약 26만 평)이며, 올해 3월 말 기준으로 약 4천 200명의 임직원이 재직하고 있다. 1979년에 준공돼 현재 9개 차종을 생산하고 있으며 연간 약 25만 대의 생산 능력을 확보하고 있다. 일반적으로 생산 동선이 ‘ㄷ자’ 형태를 한 다른 공장들과는 달리 평택 공장은 ‘ㄴ자’ 형태를 하고 있는 것이 특징이다. KG 모빌리티 측은 과거의 설비를 최대한 효율적으로 사용하기 위한 노력의 결과라고 밝혔다.
이런 평택 공장이 최근 변화를 겪었다. 지난 10월 중순부터 2개월간 500억 원을 투자해 모노코크(monocoque·차체와 프레임이 하나로 된 구조)보디 차종을 생산하는 조립 2라인과 보디 온 프레임(프레임 위에 차체가 조립되는 구조)차종을 생산하는 조립 3라인을 통합한 것이다. 공사 마무리 이후 혼류 라인 운영이 가능해짐에 따라 생산 라인의 유연성이 확보됐으며, 이에 따라 수요에 맞춰 운영 효율을 극대화 할 수 있다고 밝혔다.
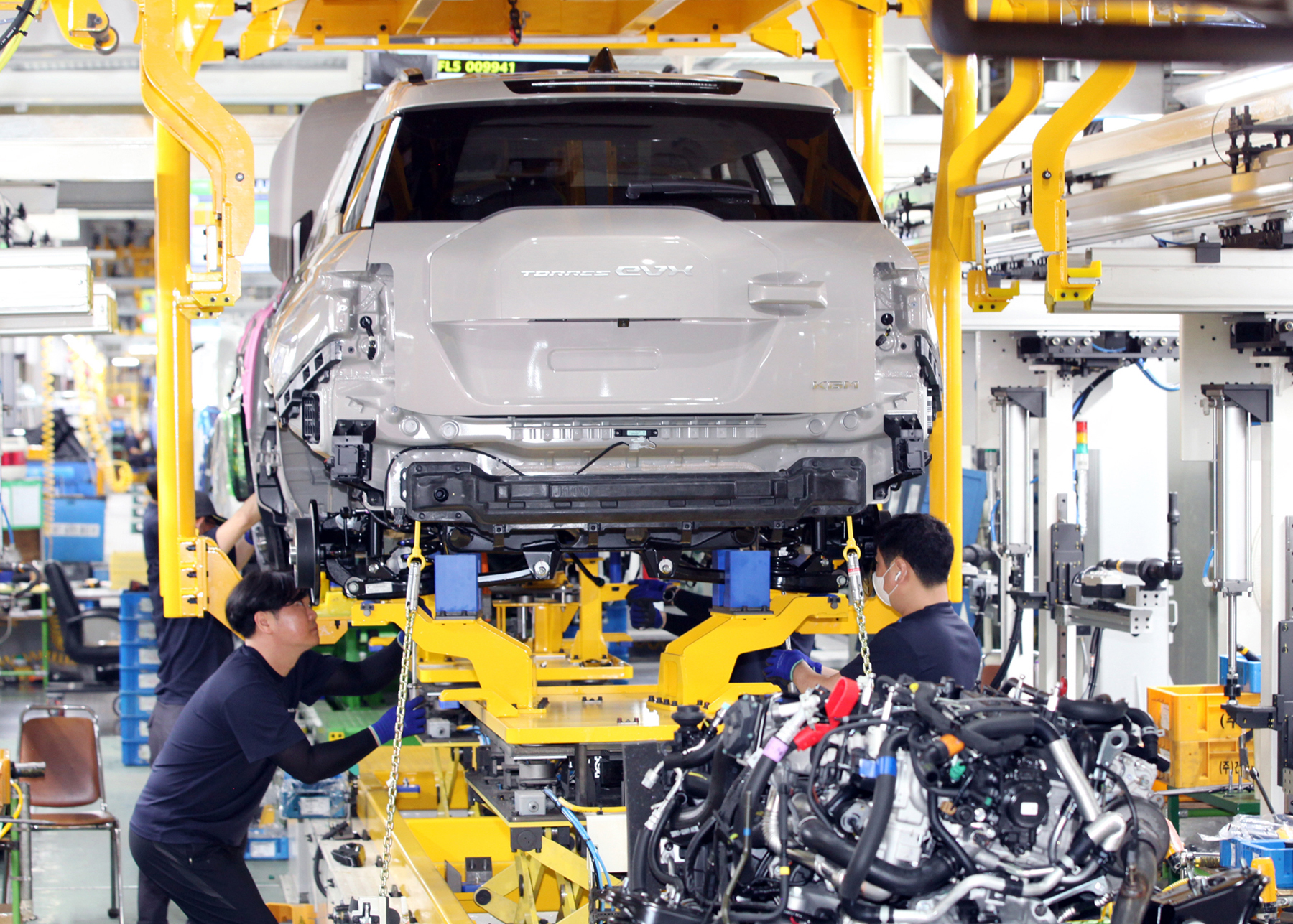
조립 3라인은 기존 조립 2라인과의 통합으로 혼류 생산이 가능하며, 보디 온 프레임인 ▲렉스턴 ▲렉스턴 스포츠 ▲렉스턴 스포츠 칸, 모노코크 보디 전기차인 ▲토레스 EVX 등 총 4종의 차량을 함께 생산한다. 이에 대해 박장호 KG 모빌리티 생산본부장은 “이런 경우는 거의 유일한 사례”라고 말했다. 생산성도 크게 높아졌다. 이전에는 1시간에 22대를 생산했지만, 지금은 30대를 만들 수 있다.
대표적인 예시로는 모노코크 차종의 ‘매리지'(파워트레인 모듈과 차체의 위치를 자동으로 맞춰 하나로 합치는 것)공정과, 보디 온 프레임 차종에 적용되는 ‘보디 마운트'(엔진과 내부 장비가 조립된 차에 차체를 덮는 것)공정을 하나의 라인에서 할 수 있다는 것이다.
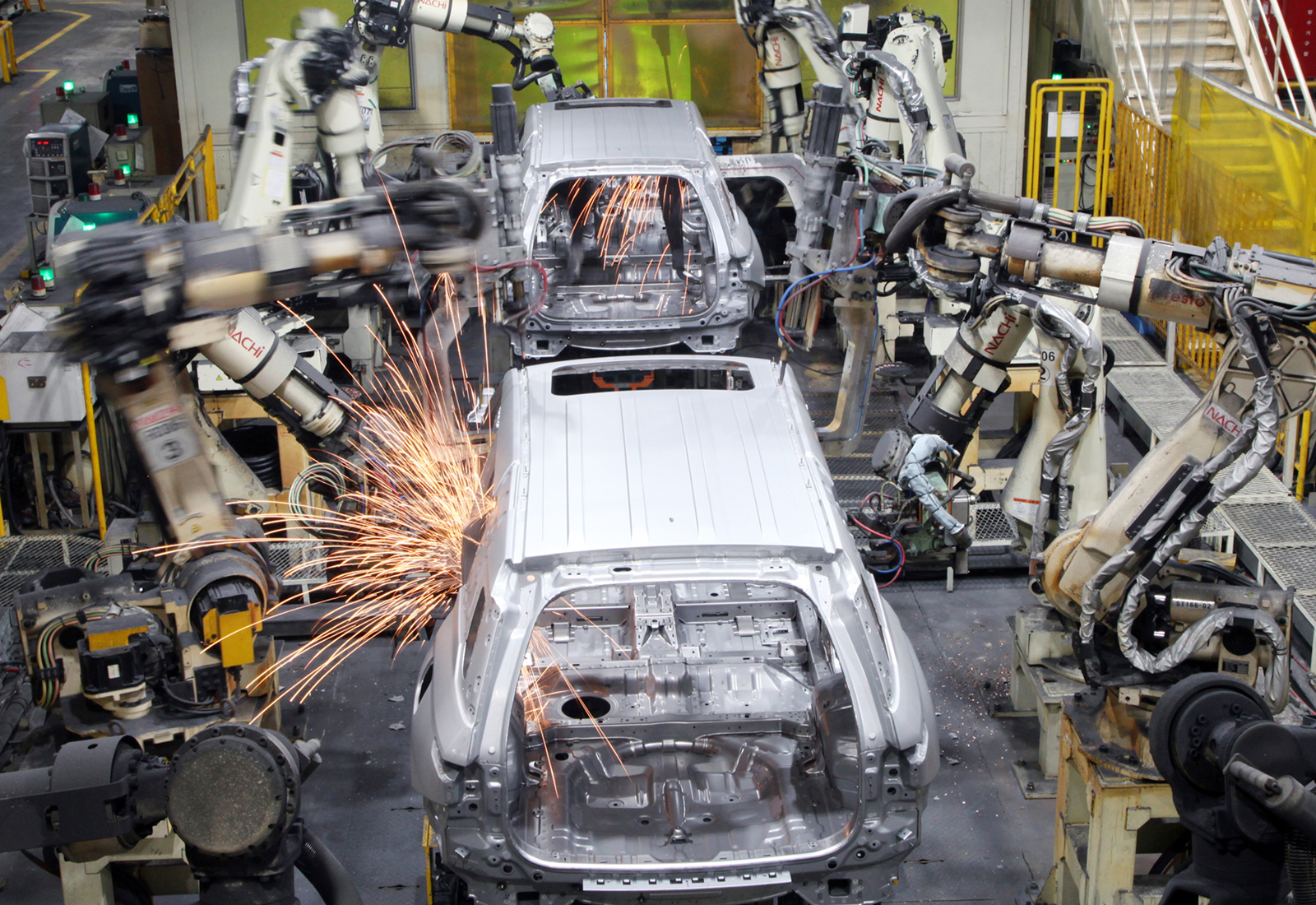
차체 1라인은 복층 구조로 1층은 생산, 2층은 품질 검사가 진행된다. 가동률은 약 92%로 시간당 28대, 연간 5만 1500대가 생산된다. 188대의 로봇과 104대의 지그(가공물 또는 조립물을 특정 위치에 위치하게 하는 것)가 작업을 진행하며, 작업자들은 미세 조정, 품질 확인과 같은 세부 직업을 진행한다. 안종석 차체1팀 책임매니저는 “차체 라인은 조립 라인에 비해 자동화율이 높은 편”이라며 “용접과 이송은 로봇이 100% 진행하고, 볼팅(볼트를 조이는 작업)은 70% 정도 수행한다”고 설명했다.
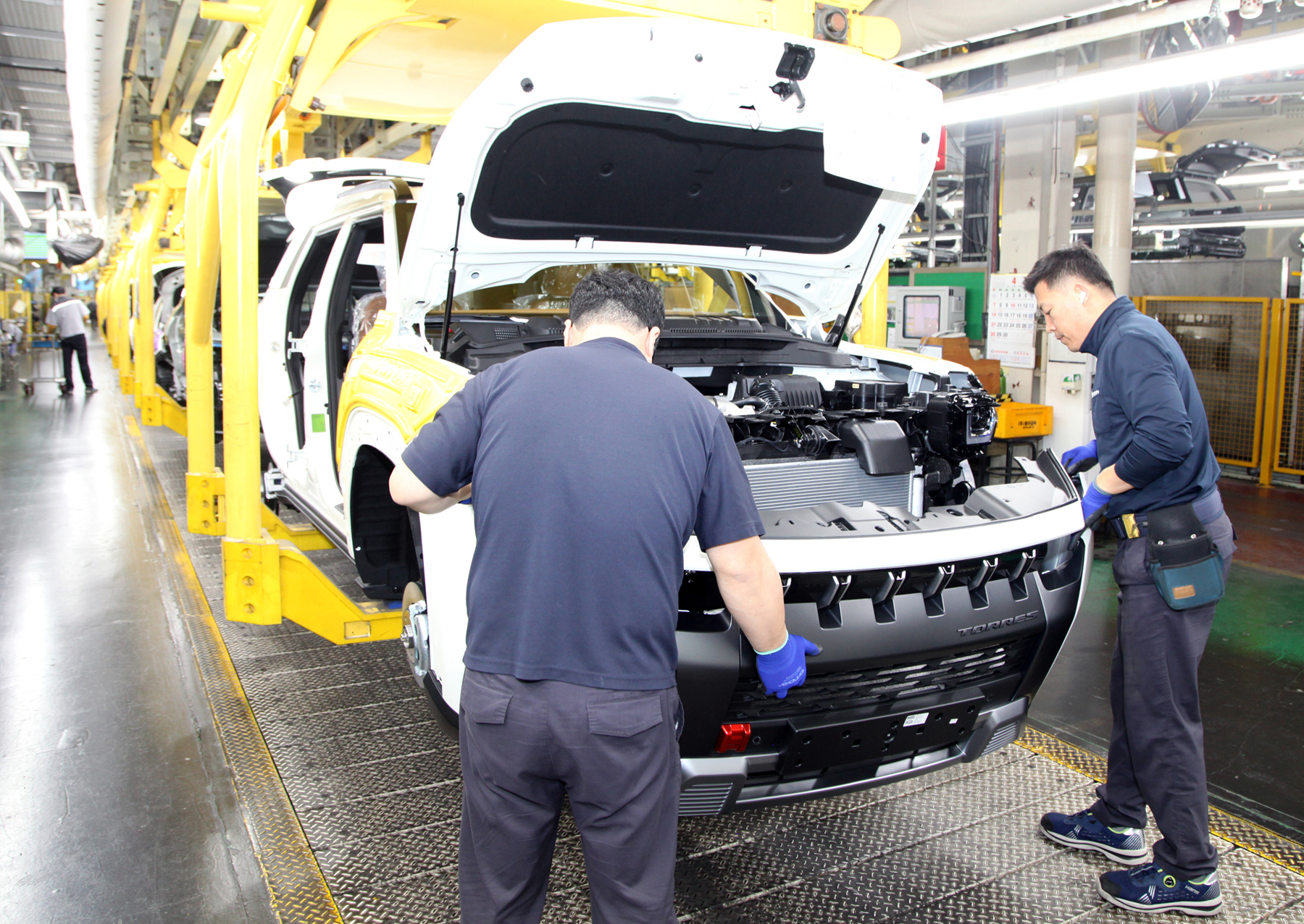
마지막으로 방문한 조립 1라인은 원래 보디 온 프레임 차량을 생산했지만 2010년에 모노코크 보디 차량의 생산을 위해 개조 작업을 거쳤다. 이곳에서는 ▲티볼리 ▲티볼리 에어 ▲코란도 ▲코란도 EV ▲토레스 ▲토레스 EVX 등 6개 차종을 생산한다.
이곳에서 전기차 배터리의 자동화된 장착 설비를 볼 수 있었다. 정해진 조립3팀 책임매니저는 “배터리 중량이 400㎏이 넘기 때문에 사람이 작업할 경우 크게 위험할 수 있어 자동화를 진행한다”고 설명했다.
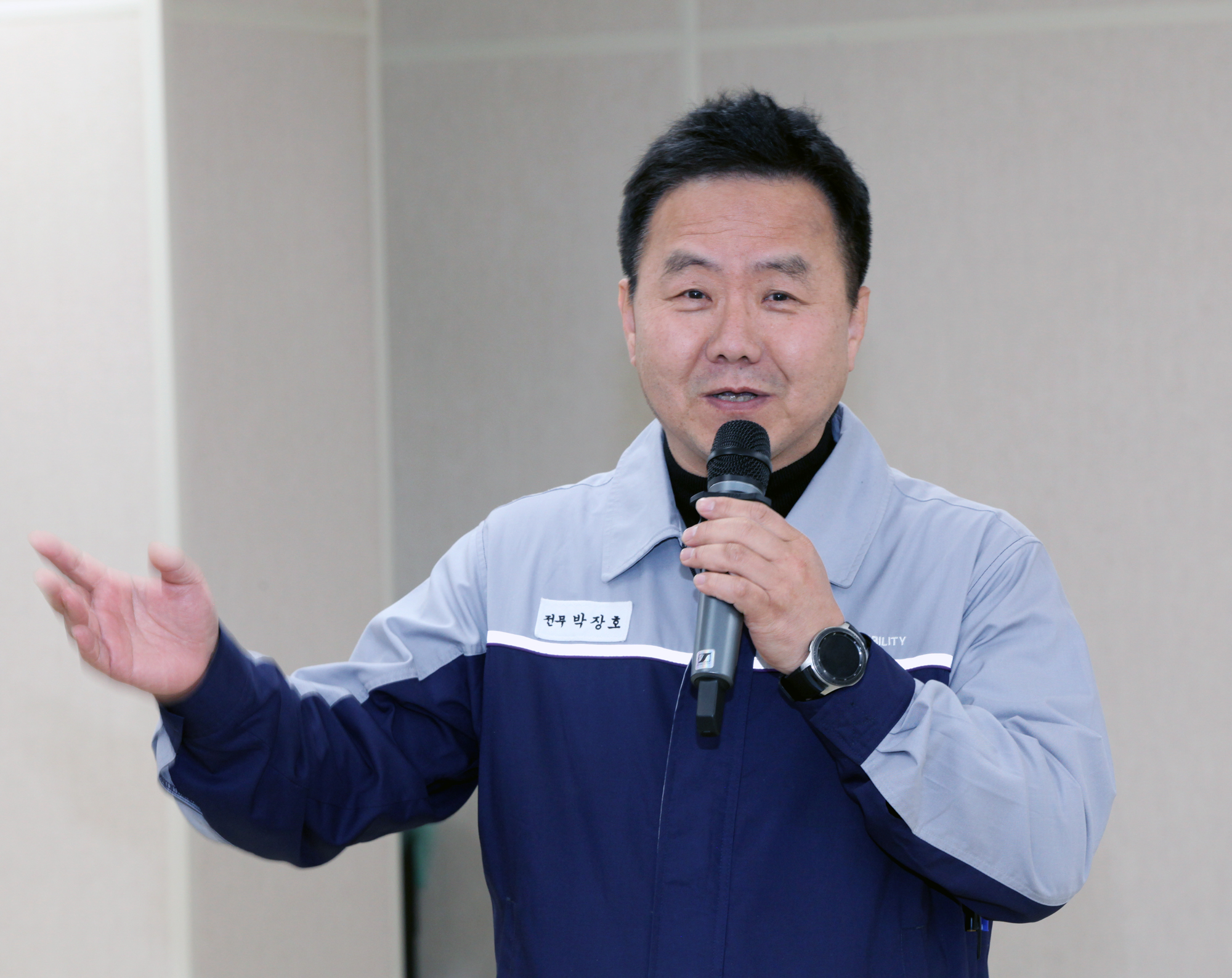
박장호 KG 모빌리티 생산본부장은 “평택 공장은 특별히 좋거나 새로운 설비를 들여온 곳은 아니지만, 차는 설비가 아닌 구성원들이 만드는 것이다”라며 “공장 직원들은 고객들을 제품(완성차)로 만난다는 마음으로 최선을 다하고 있다”고 밝혔다. 이어 “더욱 치열하게 토론하고 해답을 찾아 끊임없이 발전할 것”이라고 말했다.
- 벤츠 코리아, 본사·딜러사 불 다 꺼진다… 지구의 날 맞아 활동 시작
- 이번 1분기도 흑자! KG 모빌리티, 2년 연속 1분기 흑자
- 도심에서도 스릴 넘치게! 콘티넨탈, ‘맥스콘택트 MC7’ 출시
- 포르쉐코리아, 사회공헌 캠페인 ‘퓨처 헤리티지’ 수여식 진행
- 폴스타, 쿠페형 전기 SUV ‘폴스타 4’ 6월에 드디어 국내 출시